Преобразование швейной фабрики HUGO BOSS Izmir в "умное" производство
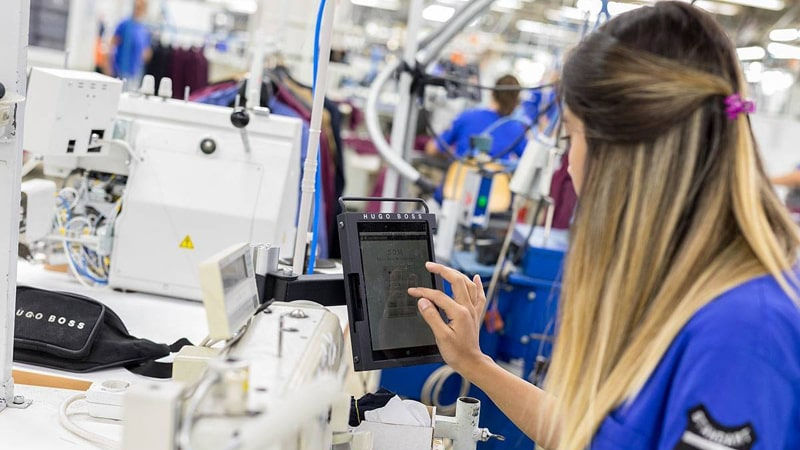
Швейная фабрика HUGO BOSS Izmir - крупнейшая собственная производственная площадка HUGO BOSS. Она была основана в 1999 году и имеет площадь 65 000 кв. м. На предприятии работает около 4 000 человек. Годовой объем производства достигает 900 000 костюмов, 2 000 000 рубашек и 550 000 единиц женской одежды.
В рамках своей стратегии, направленной на более эффективное удовлетворение высокодинамичных запросов клиентов, HUGO BOSS Izmir разработала концепцию "умной фабрики" Industry 4.0, которая стала центром промышленной трансформации предприятия.
На заводе используется более 1600 планшетов (с поддержкой WiFi-соединения), которые помогают руководству отслеживать любые данные в режиме реального времени.
Реализация концепции Индустрии 4.0
HUGO BOSS Izmir начал преобразовывать свое производство в умную фабрику в 2015 году и сейчас это предприятие можно назвать примером реализации концепции Индустрии 4.0 на швейных фабриках.
На предприятии используются AR/VR, облачные вычисления, аналитика данных, ИИ, IoT и ML. С их помощью HB Izmir смогла добиться значительного снижения затрат, быстрого времени выполнения заказа, гибких процессов, минимальной сложности, легкого получения данных в любой момент времени, улучшения качества и повышения производительности.
По словам Эркута Экинчи, руководителя отдела ИТ компании HB Izmir, фабрика смогла превратиться в "умную фабрику" с четырех точек зрения - стратегической, тактической, технической и методологической. Для этого была создана цифровая сеть между людьми, машинами, продукцией и процессами предприятия, что позволило создать "цифрового двойника" завода.
Процесс преобразования был разбит на три этапа - 2015-2016 гг, 2017-2018 и 2019-2020. В составе проектов по преобразованию:
Интеллектуальное управление данными (SDM)
На заводе используется более 1600 планшетов (с поддержкой WiFi-соединения), которые помогают руководству отслеживать любые данные в режиме реального времени. С их помощью собирается и отображается любая информация, связанная с производством, качеством работы в режиме реального времени. Они являются двунаправленным инструментом управления цехом и позволяет отслеживать KPI в режиме онлайн.
Групповая доска и линейная доска
В отличие от традиционных заводов, где доски в цехах ведутся вручную, в HB Izmir это делается в цифровом формате, чтобы каждый сотрудник завода мог быть в курсе событий в режиме реального времени. Групповая доска - это доска для отслеживания информации группы из примерно 10-15 рабочих, которые вместе работают над определенным проектом, а линейная доска предназначена для отслеживания данных всех производственных линий, складов, инвентаря и т.д. Все машины взаимосвязаны друг с другом, и эти доски отображают эффективность работы одного оператора, всей линии, всего цеха; дефекты качества, обновление запасов/инвентаря в реальном времени, информацию об отгрузке продукции и производительность группы.
Дополненная реальность (AR)/виртуальная реальность (VR)
На HB Izmir AR и VR используется для мягкого обучения операторов, интеграции процессов качества, информации о продукции и машинах. Например, на фабрике разработаны AR-планшеты, которые помогают операторам получать изображение машины. После захвата изображения планшет использует это виртуальное изображение и воспроизводит видео процесса технического обслуживания и смазки этой машины, так что оператор может понять весь процесс самостоятельно. Это обучение также возможно благодаря HB Izmir путем сканирования QR-кода машины в планшете.
VR также используется для усовершенствования и цифровизации процесса обучения разработке продукции. На экране VR-планшета отображается список продуктов и перечень операций в каждом продукте. Затем для каждой операции может быть воспроизведено видео, чтобы операторы могли понять критические моменты конкретного продукта. После просмотра видео оператору необходимо пройти экзамен, анкета которого появляется на экране планшета. Если оператор не справляется с экзаменом, ему необходимо повторно просмотреть видео, пока он не достигнет совершенства в учебных модулях.
Активная цифровая помощь (ADA)
Эта система отслеживает и извлекает все данные о заводе. С помощью чатбота сотрудник может спросить что угодно о конкретной производственной линии, цехе, отгруженных заказах, готовых к отгрузке заказах и качестве, чтобы получить нужную информацию в кратчайшие сроки.
Распознавание речи
Каждый раз, когда покупатель размещает новый заказ, команде разработчиков и дизайнеров необходимо определить технологический процесс. Соответствующие лица просто смотрят на образцы одежды и пытаются создать поток модели (поток дизайна) путем ввода данных о сотнях различных операций. Обычно эти данные вводятся вручную, и это тяжелая задача. Для оптимизации процесса была внедрена технология распознавания речи, когда оператор говорит об определенном продукте/операции, планшет распознает слова, произнесенные оператором, и затем раскрывает всю информацию. Это экономит 2-3 часа на каждом новом SKU при определении потока операций.
Еще одной из инициатив является прогнозирование дефектов качества с помощью искусственного интеллекта. Завод способен изучать исторические данные и прогнозировать возможные дефекты в работе и продукции. Утверждается, что 80 процентов дефектов могут быть выявлены с помощью искусственного интеллекта и анализа данных. ИИ просматривает все дефекты, которые имели место в прошлом во всех SKU, над которыми работала фабрика, и определяет, кто был ответственен за эти дефекты, на каких линиях эти дефекты возникли и когда они возникли. Этот процесс позволяет спрогнозировать количество дефектов в любом текущем проекте и помогает заблаговременно принять решение.
Аналогичным образом, на участке раскроя HB Izmir использует ИИ и машинное обучение для "предварительного распознавания" возможных дефектов в деталях авторезаков.
Еще одно улучшение было сделано в области управления персоналом. Проект Oxygen использует ИИ для выявления низкоэффективных работников в цехе завода путем анализа исторических данных операторов и определения тенденции их эмоций. Как только эмоции человека улавливаются, руководство завода разрабатывает план по повышению его/ее производительности.
Система 3D Space planning - автоматическая транспортная система, которая устраняет необходимость транспортировки рабочих и машин из раскройного отдела в различные сегменты, увеличивает использование объема за счет сохранения запасов резки в воздухе и обеспечивает экономию пространства. С помощью этой транспортной системы полуфабрикаты, из которых формируется пиджак, автоматически транспортируются к сегментам производства, таким как воротник, треугольник, нагрудный карман, чехол, спинка и подготовка пластин в соответствии с последовательностью производственного плана.
Проект A1+ направлен на сокращение использования ткани, которая является наиболее затратной частью производства мужской одежды, с помощью алгоритмов машинного обучения. Для этого использовались данные по оптимизации ткани, которые формировались на фабрике Hugo Boss İzmir в течение 20 лет.
Отмечается, что фабрика Hugo Boss İzmir, которая производит около 4 миллионов единиц продукции в год смогла с помощью алгоритма показать лучшие показатели оптимизации, сэкономив 2% ткани на единицу продукции, по сравнению с расчетами людей.
https://apparelresources.com/technology-news/manufacturing-tech/industry-4-0-technologies-apparel-manufacturing-challenges-ahead/