Контроль состояния конвейерной ленты на горнодобывающих предприятиях ЕВРАЗ с помощью системы видеоаналитики Vizorlabs
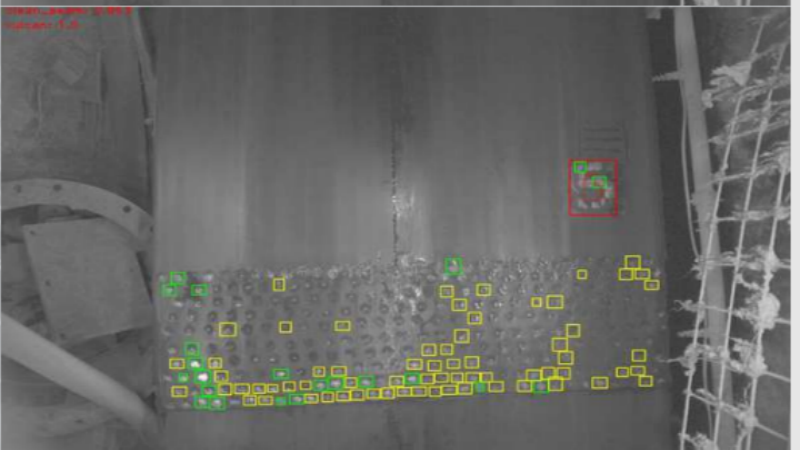
На горнодобывающих комплексах компании ЕВРАЗ для транспортировки горных материалов используется ленточные конвейеры. На каждой шахте предприятия может использоваться до 6-8 конвейеров.
Безостановочная эксплуатация конвейеров является одной из важных задач предприятия, поскольку любая критическая остановка приводит к снижению выработки и, как следствие, уменьшению доходов предприятия.
Для контроля одного из основных узлов конвейера, транспортной ленты, перед началом смены мастер осуществляет обход и визуальный осмотр. Результат обхода он заносит в журнал осмотра, на основании которого проводятся планово-предупредительный ремонты (ППР). В случае обнаружения критического состояния стыков, полотна ленты вызывается ремонтная бригада и производится остановка конвейера для ремонта.
Компания искала решение, которое могло бы избавиться от проблем возникающих при проведении ТОиР конвейерных лент:
- длительное время диагностики (до 2 часов на осмотр);
- низкая оперативность (критические повреждения выявляются слишком поздно);
- высокий риск аварий (разрывы ленты на работающем конвейере);
- отсутствие диагностики нижней части ленты;
- невозможность оптимизации графика ППР и минимизации простоев.
Идея состояла в том, чтобы автоматически отслеживать состояние ленты на всех конвейерах используя возможности видеоаналитики.
Использование ИИ в системе видеоаналитики
Компания ВизорЛабс внедрила на ЕВРАЗ программно-аппаратный комплекс автоматической диагностики и мониторинга состояния конвейерной ленты, состоящего из камер мониторинга, программного модуля видеоаналитики с искусственным интеллектом, модуля отчетов и пользовательского интерфейса.
На каждом конвейере были размещены взрывозащищенные камеры высокого разрешения, направленные на участок конвейера, свободный от горной массы. В круглосуточном режиме камеры снимали проходящую под ними ленту и формировали полный снимок конвейера каждые 30 минут.
Предварительно при настройке комплекса была произведена разметка снимка, где фиксировалось состояние ленты (ширина на разных участках, наличие разрывов на краях), количество и состояние стыков (число заклепок на каждом стыке).
Изображение с камер поступало на сервер видеоаналитики, где нейросеть анализировала каждый новый снимок конвейерной ленты и отдельных стыков: сравнивала новый снимок с "эталоном", загруженным в систему, а каждый последующий – с предыдущим снимком.
По результатам сравнения система автоматически фиксировала изменения (повреждения ленты, ширина ленты, количество заклёпок на стыках) и заносила их в отчет, который через веб-интерфейс в режиме реального времени был доступен мастеру участка. В случае обнаружения критических повреждений ленты система автоматически отправляла уведомление мастеру на e-mail или push/sms уведомление на мобильное устройство, а также, при наличии соответствующих настроек, могла экстренно остановить конвейер.
В результате внедрения комплекса были реализованы функции:
- онлайн просмотра состояния ленты конвейера;
- контроля состояния и износа стыков (подсчет количества заклепок, ширина полотна, разрывы на краях) с фото-подтверждением;
- формирования сводного отчета по состоянию стыков и отдельных фрагментов ленты с динамикой изменений;
- ведения истории событий (изменений состояния) по каждому фрагменту и стыку ленты с фото-подтверждением;
- автоматического уведомления о критическом износе стыков или отдельных фрагментов ленты;
- синхронизации с информацией о ремонтах ленты для "обнуления" состояния стыков;
- предиктивной аналитики по скорости износа стыков и ленты для планирования ремонтов;
- доступа через web-интерфейс с любого компьютера корпоративной сети;
- интеграция с ERP системой предприятия.
Внедрение системы видеоаналитики позволило:
- сократить трудозатраты на осмотр конвейерных лент на 2 часа в сутки на один конвейер;
- повысить точность и оперативность контроля дефектов ленты;
- оптимизировать график ремонтов (остановка не более одного конвейера за раз);
- сократить время ремонтов за счет не сложных профилактических ремонтов;
- повысить производительное время;
- увеличить объемы выпуска продукции;
- снизить себестоимости продукции.