Машинное зрение для обеспечения прослеживаемости производства автокомпонентов
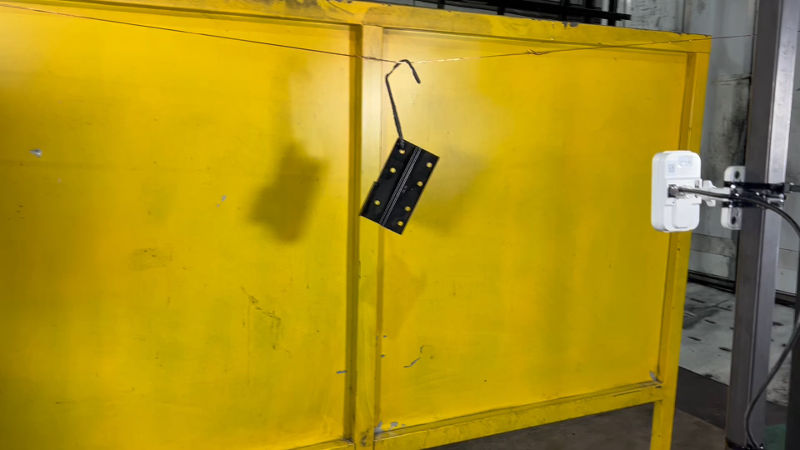
ООО «АвтоМаш» является официальным заводом-доработчиком продукции АЗ ГАЗ. Компания производит автофургоны и специальную технику, а также выполняет модернизацию автомобилей ГАЗ.
Перед предприятием стояла задача – увеличить эффективность работы по сборке продукции и повысить прослеживаемость деталей на производстве.
В рамках решения этой задачи проблемой стал недостаточный уровень цифровизации процессов на предприятии: задания для рабочих формировались в бумажном виде, отчеты о выполнении заполнялись вручную после смены. Кроме того, разнообразие очень похожих друг на друга деталей, усложняло их идентификацию для сотрудников. Еще одно проблемой было то, что материал, поступающий на склады, регистрировался в системе учета, но его дальнейшее использование не отслеживалось полностью. Регистрировались только готовые изделия, которые поступали в цех сборки.
Идея решения заключалась во введении цифровых журналов, создании автоматизированных рабочих мест (АРМ), а также поста с видео-камерой для распознавания деталей с помощью машинного зрения.
Для решения задачи по отслеживаемости производства команда специалистов ООО «АвтоМаш» и АО «Моделирование и цифровые двойники» (АО «МЦД») запустили пилотный проект. В его рамках была создана база данных комплектующих, внедрены цифровые журналы с заданиями, оборудованы автоматизированные рабочие места (АРМ), организован стационарный пост обнаружения деталей после покраски, для операторов создан журнал событий и объединенный инфоцентр для руководителей.
Работа над системой началась после проведения необходимого технического осмотра и предпроектного обследования предприятия, а также сбора необходимых данных – каталога деталей, 3D-моделей, фото и видео материалов.
При этом существовал ряд сложностей. Так, модель, разработанная специалистами АО «МЦД», не была типовой, поскольку она различает не разносторонние, а похожие объекты. Кроме того, в процессе обучения модели требовалось большое количество ручной разметки для правильной идентификации деталей.
Система, созданная в рамках пилотного проекта, позволила сотрудникам самостоятельно заполнять каталоги деталей.
Для прослеживаемости процесса получения деталей были использованы определенные метрики – например, руководство может видеть метрики производства деталей, определять, на каком этапе находится их производство, а также понимать, какое количество уже изготовлено.
Операторы могут отследить этап изготовления детали. Для каждой из них есть свой маршрут, состоящий из лазерной резки для заготовки, гибки металла, дробеструйной обработки, покраски и снятия деталей. На последнем этапе определяется артикул детали с помощью камеры и системы машинного зрения.
Вся информация, касающаяся этапов изготовления детали и степени ее готовности, заносится в цифровые журналы. Журналы хранятся в цифровых базах данных и могут быть отфильтрованы, экспортированы и использованы для формирования отчетов. В конце используется общий журнал под названием «Инфоцентр» – в нем фиксируются полностью готовые детали, позволяя определить их количество.
Система также ориентирована на помощь новым сотрудникам предприятия, не знакомым с номиналами всей продукции, выпускаемых компанией. Используя это решение, они смогут выявлять правильную продукцию и отправлять в нужное место на складе. Так, система позволяет добавлять комментарии к маршрутам деталей в том случае, если она идет по особым критериям. Эти подсказки помогают новым сотрудникам и упрощают работу.
В процессе составления карты текущего состояния на потоке изготовления «сэндвич-фургона» был выявлен ряд проблем на участках окраски, гибки и лазерной резки металла: отсутствие прослеживаемости между участками; лишние затраты времени на поиск деталей после окраски; отсутствие оперативной и достоверной информации у руководителей участков о выпуске комплектующих в реальном времени.
Разработка цифровых журналов привела к более оптимизированному рабочему процессу, что позволило лучше использовать ресурсы и повысить производительность.
По оценке экспертов АО «МЦД» "внедрение системы машинного зрения увеличит эффективность работы предприятия на 25%". Специалисты «АвтоМаш» отметили снижение времени протекания процесса (ВПП) на 28,3% и показателя незавершенного производства в потоке на 50%, а также повышение выработки на человека на 13,1%.
В перспективе компании рассчитывают запустить крупный проект по цифровизации. Сейчас система работает как цифровой журнал для каждого отдельного АРМ. В будущем ожидается, что они будут связаны между собой через сменное задание. Предполагается, что в будущем у каждого оператора будет планшет с установленной системой, на который будет приходить сменное задание, с указанием операции, которую нужно выполнить.